High Quality High temperature Melting/ heating furance for LPG cylinder
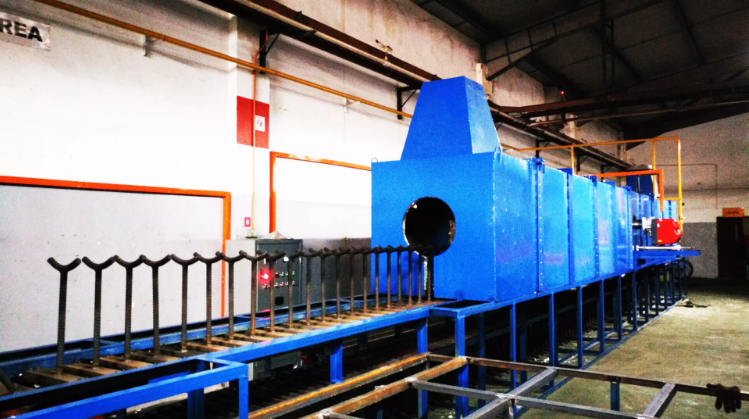
Product Description
After a period of use, the paint on the surface of the cylinder will peel and peel off, thus causing the surface of the cylinder to rust and corrode. After the expiration of use, the surface of the cylinder must be thoroughly cleaned and repainted at the same time as the inspection. At present, due to the use of electrostatic spraying technology, the firmness of the paint film has been further improved, and some paint films are difficult to remove by shot blasting. In order to completely remove the paint film on the steel cylinder, only through the heat treatment furnace, the paint film on the surface of the steel cylinder is burned into charcoal or ashes. This makes it easy to remove any remaining paint from the surface, creating good conditions for blast cleaning and repainting.
Machine name | Heat treatment furnace for LPG cylinder |
Production speed | 75~300 cylinders/hour |
Feeding type | chain drive feeding |
Size of cylinder | 320*700~420*1250mm |
Max. pressure | 25Mpa |
Max. temperature | 600~1200℃ |
Dimensions | 12500*1390*1560mm |
Weight | 12ton |
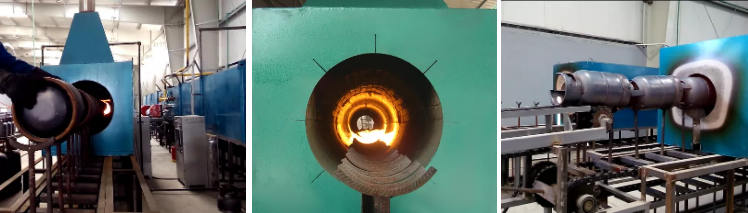
Machine Configuration
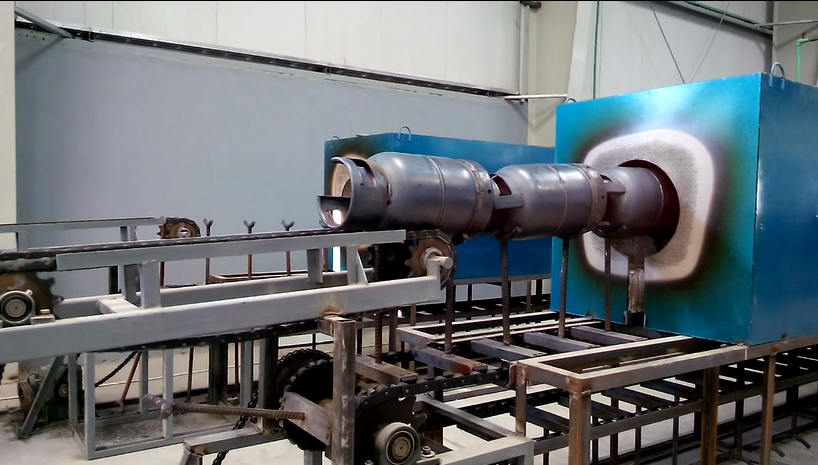
A. Normalizing Furnace
1.Continuous heat treatment furnace: total length for this machine is 20 meters(furnace is 15 meters, loading & unloading holder is 5 meters). The furnace is welded by high quality section steel, the furnace is lined with high temperature resistant high alumina refractory firebrick, insulation layer is made of fiber and other thermal insulation materials. Overall, the high temperature furnace is light and of good insulation performance.
2.Application: Cylinder normalizing heat treatment
3.Specification: ISO Standard, cylinder weight:6kg/pc, 12.5kg/pc,25 and 52kgs Diameter of cylinder is from DN200-400mm
4.Working efficiency: 200pcs/hour
5.Entrance temperature: 30ºC
6.Cylinder heating temperature: 900ºC±25ºC
7.The max. working temperature of the furnace body: ≤1000ºC
8.The temperature rise of furnace body surface is according to China industry standards.
9.Parts of the furnace:
10.Horizontal furnace body: 1 set
11.Loading and unloading chain mechanism: 1 pair
12.Nature gas control system(record containing): 1 set
13.Flue gas and heat exchange system: 1 set
14.Fuel type: nature gas
15.Fuel calorific value: 8500 Kcal / kg
16.The form of combustion apparatus: high-speed fuel burner
17.Heating quantity and thermal load distribution: 8 pcs gas burner
18.No. of burners in heating section:4 pcs burners, 230KW/pcs
19. No. of burners in the front of temperature holding section : 2 pcs burners, 230KW/pcs
20. No. of burners in the back end of temperature holding section : 2pcs burners, 150KW/pcs
21.Power supply: 20KW, 380V, 50Hz
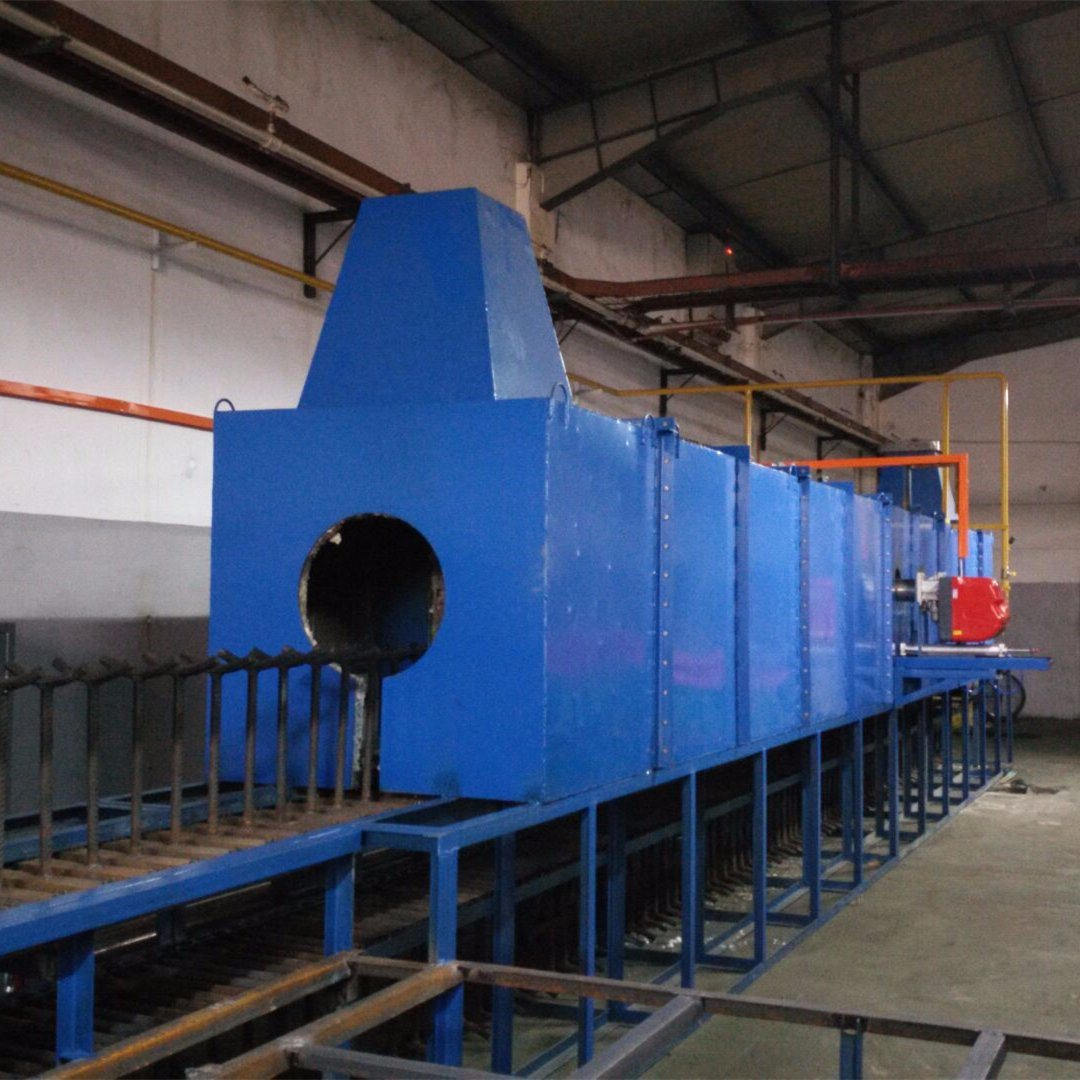
B: Annealing Furnace
1. No of burning nozzle: 150000Kcal, totally 8 pieces.
2. Working temperature: 700 ± 25 degree
3. Furnace chamber
A.Furnace length: 32.5m, overall length including loading & unloading: 37.5m.
Furnace liner lower part is high-temperature cast structure, upper part is heavy brick or cast module. Between the furnace body
and furnace liner is insulating layer made from Aluminum silicate fiber cotton. To ensure the ability of keeping the temperature.
B.Each section of furnace: L2500*W1350*H1450mm, inner hole size 650mm.
C.Out shell is made from angle iron and steel sheets. The bottom is made from steel structure, channel steel, with steel sheets,
due to the high pressure.
Between each section of furnace, they are connected by angle steel flange, easy to install and adjust.
Installation
1. The user should make the equipment foundation according to the civil information and drawings supplied by supplier, strictly meeting to all requirement in drawings.
2. The fire furnace is made by subsections. When install, you should put the all sections of furnace onto the earth pits, jointing face by face in plane (on the butt joint place, please put the silica acid aluminum pads), pay attention to the installation level surface and the butt joint line.
3. Fix the conveying unit on the setting position according the inlet/outlet positions shown in the installation sketch and the civil information drawings.
4. Install the oil supply and gas supply pipelines and burners.
5. Install the control system, after installation, carry out the test running. Observe the conveying motor running direction whether it is correct or not, the convey unit should run smooth without block.
6. Install the smoke removing system according to the site requirement.
Process Display
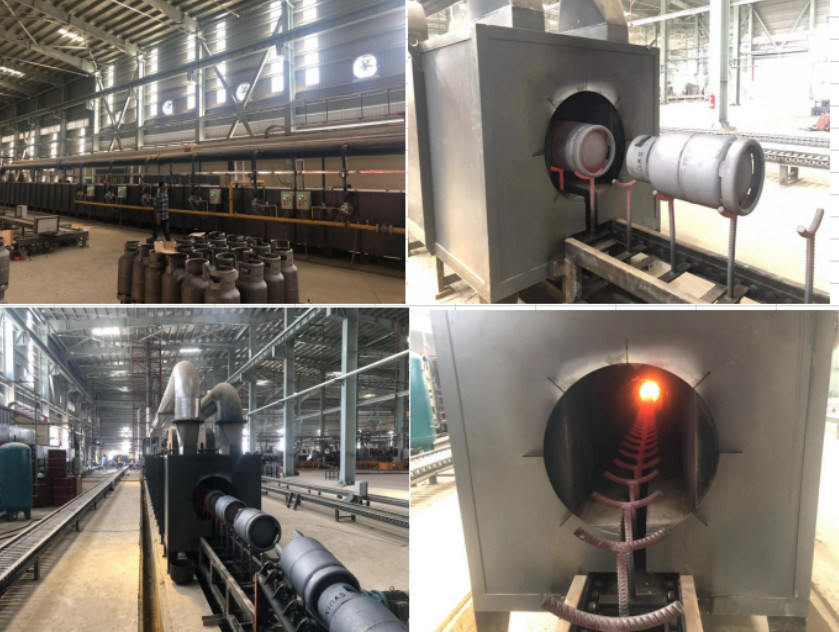
FAQ
Q: What size of LPG cylinder your machine can produce?
A: 6kg, 12kg,15kgs and 50kgs LPG cylinder for cooking and other size according customers’ requirement.
Q: Can you design machines according LPG cylinder technical drawing?
A: Sure, please send your technical drawing to us.
Q: What are the benefits to choose your machines?
A: Our machines are strong and reliable for long term industrial manufacturing
We need to know following information to quote you correct machines:
1.Technical Drawing of the cylinders you want to make?
2.What size of cylinder you want to produce?(such as 6kg, 12kg)
3.What diameter and thickness of the cylinder you want to make?
4.Are you new in this area or you already have some machines in the workshop?
5.Capacity you require, i.e. how many pieces and sizes you want to make per day?